Let's look at the basics of CTM manufacturing, the role of quality by design in the CTM manufacturing process, and the benefits you can expect when you partner with a trusted CDMO like UPM Pharmaceuticals for your clinical manufacturing needs.
- What is Clinical Trial Material Manufacturing?
- What Are Clinical Trial Materials?
- Aligning Current Good Manufacturing Practice (cGMP) Guidelines with Clinical Manufacturing Processes
- Manufacturing Processes
- Routes of Delivery
- Phases of Clinical Studies
- The Role of Quality by Design in CTM Manufacturing
- Benefits of Specialty CTM Manufacturing Services from UPM Pharmaceuticals
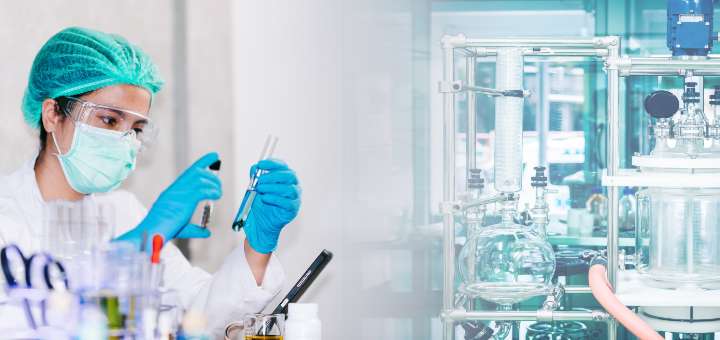
What is Clinical Trial Material Manufacturing?
Clinical trial material manufacturing is a specialized form of pharmaceutical manufacturing focusing on creating drugs that will be used for clinical research. Working with clinical trial materials requires special manufacturing processes and careful attention to detail to ensure safety and security.
What Are Clinical Trial Materials?
Clinical trial materials (CTM) are pharmaceuticals that are in a finished form suitable for administration to clinical trial participants but not intended for commercial sale. Before manufacturing clinical trial materials, a plan and timeline must be created to help guide you through the development and clinical trial process. An experienced contract development and manufacturing organization (CDMO) like UPM Pharmaceuticals is able to provide valuable insight into a realistic timeline for developing and releasing a new drug.
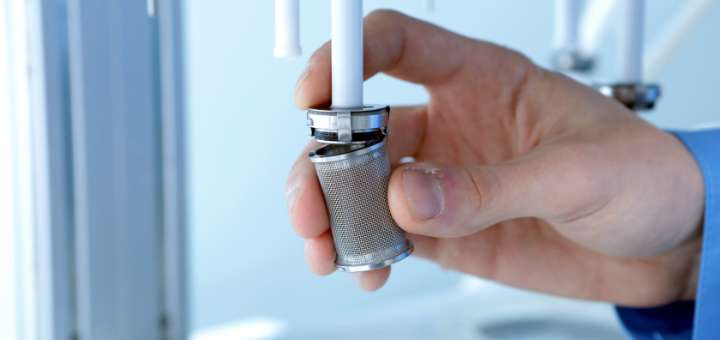
Aligning Current Good Manufacturing Practice (cGMP) Guidelines with Clinical Manufacturing Processes
When manufacturing a drug of any kind, but especially in CTM manufacturing, FDA current Good Manufacturing Practice (cGMP) guidelines must be followed closely. Improper manufacturing practices of any kind can lead to contamination, which can be costly. Biologics can not be sterilized like small molecule drugs, so the whole process needs to be sterile and managed closely.
cGMP guidelines apply to most drugs that are in phase I and II development, especially vaccines, gene therapy, recombinant and non-recombinant therapeutic products and more.
The best ways to ensure you are following cGMP guidelines are:
- 1. Have a written pharma quality control plan.
- 2. Maintain a controlled, sterile environment.
- 3. Record accurate and consistent data from the manufacturing process.
Routes of Delivery
Below are the areas that we focus on at UPM:
-
Oral (solid and liquid): Taken by mouth, either as tablets, capsules, liquids, or powders.
-
Injection: Injected through a needle and syringe. This can be subcutaneous, intramuscular, or intravenous.
-
Topical: Applied directly to the skin or mucous membranes.
-
Inhalation: Drugs are delivered to the lungs through inhalation, commonly as aerosols or dry powder.
-
Transdermal: Delivered through patches or creams applied to the skin, allowing absorption into the bloodstream.
-
Inhaled (pulmonary): Administered through inhalation into the lungs using devices such as inhalers or nebulizers.
-
Inhaled (nasal): Delivered through the nasal passages using nasal sprays or inhalers.
-
Rectal: Drugs are introduced to the body through the rectum, either as suppositories or enemas.
-
Intrathecal or Intraventricular: Delivered directly into the spinal canal (intrathecal) or ventricles of the brain (intraventricular).
-
Intra-articula: Injected directly into joints, often for the treatment of localized conditions such as arthritis.
Below are the other routes of Delivery that are available in the market:
-
Sublingual and Buccal: Drugs are placed under the tongue (sublingual) or against the cheek (buccal) for absorption through the oral mucosa.
-
Intravenous: injected directly into the bloodstream through a vein.
-
Parenteral: any route of administration that does not involve the digestive tract, such as intravenous, intramuscular, subcutaneous, or intradermal.
-
Intramuscular: injected directly into a muscle.
Phases of Clinical Studies
UPM supports all aspects of your drug product supply for Phase I, II, and III clinical studies:
Phase I
Patient Enrollment:
-
Involves 15 to 50 patients.
-
Divided into small groups known as cohorts.
Primary Objective:
-
Focus is on safety and proper dosage.
Transition to Phase II:
-
Successful completion of Phase I, with an established safe and effective dose, leads to the drug's advancement to Phase II clinical trials.
Phase II:
Patient Enrollment:
-
Typically involves fewer than 100 patients.
Primary Objective:
-
Main goal is to assess the efficacy and side effectives of the new treatment.
Transition to Phase III:
-
Successful completion of Phase II, with positive efficacy signals and manageable side effects, may lead to the decision to proceed to Phase III clinical trials.
Phase III:
Patient Enrollment:
-
Involves hundreds to thousands of patients globally.
-
Patients are randomly assigned to either the control group (standard treatment) or the study group (new treatment).
Primary Objective:
-
Test the superiority or non-inferiority of the new treatment compared to the standard treatment.
FDA Review:
-
After completion of Phase III, the FDA reviews the clinical trial results.
-
Ensures the treatment is both safe and effective for patient use.
Decision for Approval:
-
Based on FDA review, a decision is made on whether to approve the treatment for widespread use.
The Role of Quality by Design in CTM Manufacturing
The idea of Quality by Design (QbD) is credited to Dr. Joseph M. Juran. In his 1992 publication, he posited that most of the quality issues found in products were caused by a design shortcoming, so the quality of a product could be improved by improving the design from conception. Studies have shown that his theory has merit, as it is impossible to improve the quality of an improperly designed product by increasing testing.
When it comes to Quality by Design in clinical trials and CTM manufacturing, a high-quality product is one that provides its intended benefit while also being contaminant-free. To protect the general public and ensure that cGMP guidelines are maintained, the FDA strongly emphasizes the use of QbD principles by all drug manufacturers.
The fundamental principles of QbD in CTM manufacturing are:
- Determine the crucial characteristics of a drug product.
- Identify them as a critical quality attribute
- Employ process design to create a drug product that includes the critical material attributes and identifies the critical process parameters.
CONTACT US
Benefits of Specialty CTM Manufacturing Services from UPM Pharmaceuticals
Using a CDMO like UPM Pharmaceuticals can help you successfully navigate the clinical trial process and get your drugs on the market soon. Our dedicated team brings years of experience and knowledge on subjects like formulations, cGMP guidelines, clinical trial data management, clinical trial supply management, packaging and more that can help your business easily move from clinical trial manufacturing to getting the product ready for market. We offer the clinical trial services you need to achieve success.
Contact us today and find out how UPM can benefit your company.
Discover Specialized CTM Manufacturing Solutions