Dry Blending Process
The blending process greatly impacts a drug’s stability, visual appeal and ability to deliver an accurate dosage. Because dry blending is normally the first step in tablet production, a high-quality pharmaceutical mixing process is essential to ensure a uniform and effective finished dosage form.
Each drug formulation is unique, which means that no two pharmaceutical mixing processes are the same. We utilize roller compaction dry granulation to avoid using high temperatures and adding liquids, ensuring uniformity in the finished dosage form.
The dry blending process is very streamlined and uses only a few pieces of equipment compared to geometric dilution and fluid bed granulation, and it eliminates the need for separate moisture addition and material drying stages. The result of roller compaction dry granulation is a higher quality product that reduces raw material, labor and energy costs.
When choosing a pharmaceutical blending and mixing partner, make sure that they excel in the following areas:
Cleanliness
Sanitation is a core component of cleanliness, especially in the pharmaceutical industry. All surfaces of dry blending rooms must be regularly sanitized and adhere to industry guidelines that prevent equipment contamination from previously used materials and microbiological agents.
In addition, the CDMO or second source supplier must adhere to the Current Good Manufacturing Practice Regulations (CGMP) — the FDA’s regulatory standard for human pharmaceuticals which makes sure that products:
- Are safe for human consumption
- Contain all of the stated ingredients
- Are the actual strength that is stated
Process Control
The quality-assurance team should be fully engaged in the process from start to finish. They need to carefully document everything, including sanitation practices, blending processes, validation, materials sourcing and transportation details.
Protocols for test batches ensure that the same processes result in the same quality coming out of the blender every single time. Transparent processes for traceability, due diligence and audits are required for record keeping and compliance.
Equipment Selection
Mixing equipment used in pharmaceuticals production requires a higher level of complexity because its use is extremely specialized. One design or process does not fit all. Choosing the best equipment depends on the unique blending needs of your product. Depending on your specifications, different blending methods may be needed, such as roller compaction dry granulation, fluid bed granulation or dry blending.
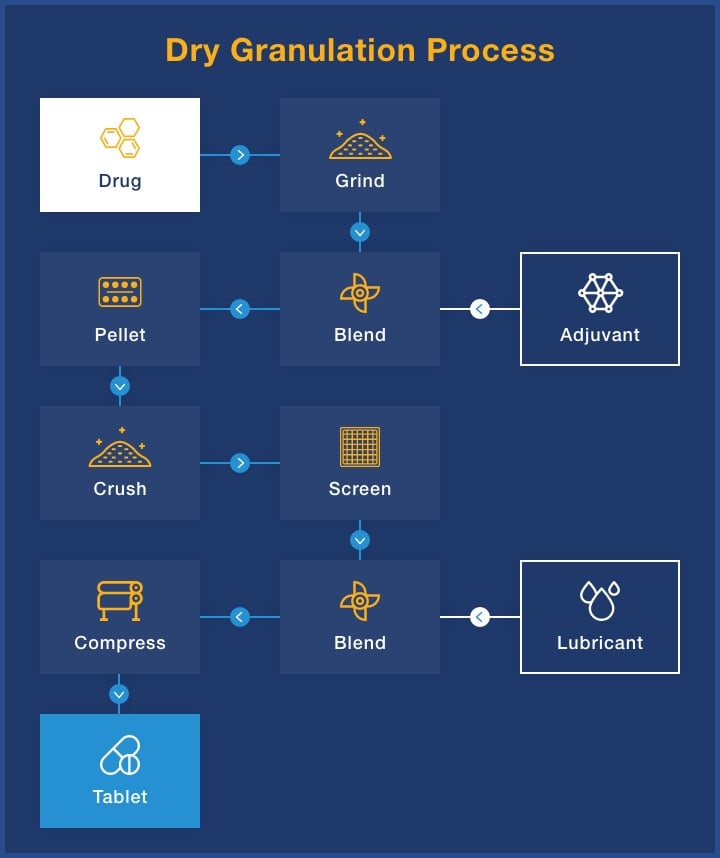
Why Choose UPM For Your Pharmaceutical Blending and Mixing?
UPM is a large-scale CDMO that specializes in pharma technology transfer and scale-up. We have years of experience successfully blending various materials, tackling different pharmaceutical mixing challenges and maintaining all required certifications. We offer the following benefits:
- Expertise - UPM has over twenty years of experience in pharma manufacturing of semi-solid and solid dose drug products.
- DEA-licensed for Schedule II–V controlled substances - We have almost 16,000 SF of DEA-approved vault space and a long-standing positive record of controlled substance manufacturing.
- Production Capabilities - Our annual production capabilities are based on one shift production:
- 700 million capsules
- 4 billion tablets
- 1,300,000 kilogram units of semi-solids
Our large manufacturing facility and warehouse allow us to handle the solid dose manufacturing demands of your project.
CONTACT US
From pharmaceutical product development through analytical testing, we specialize in personalized service, consistent quality and customization. Contact us online today or call (423) 989-8000 to learn how we can help advance your product from the laboratory to patients.
Contact Us